
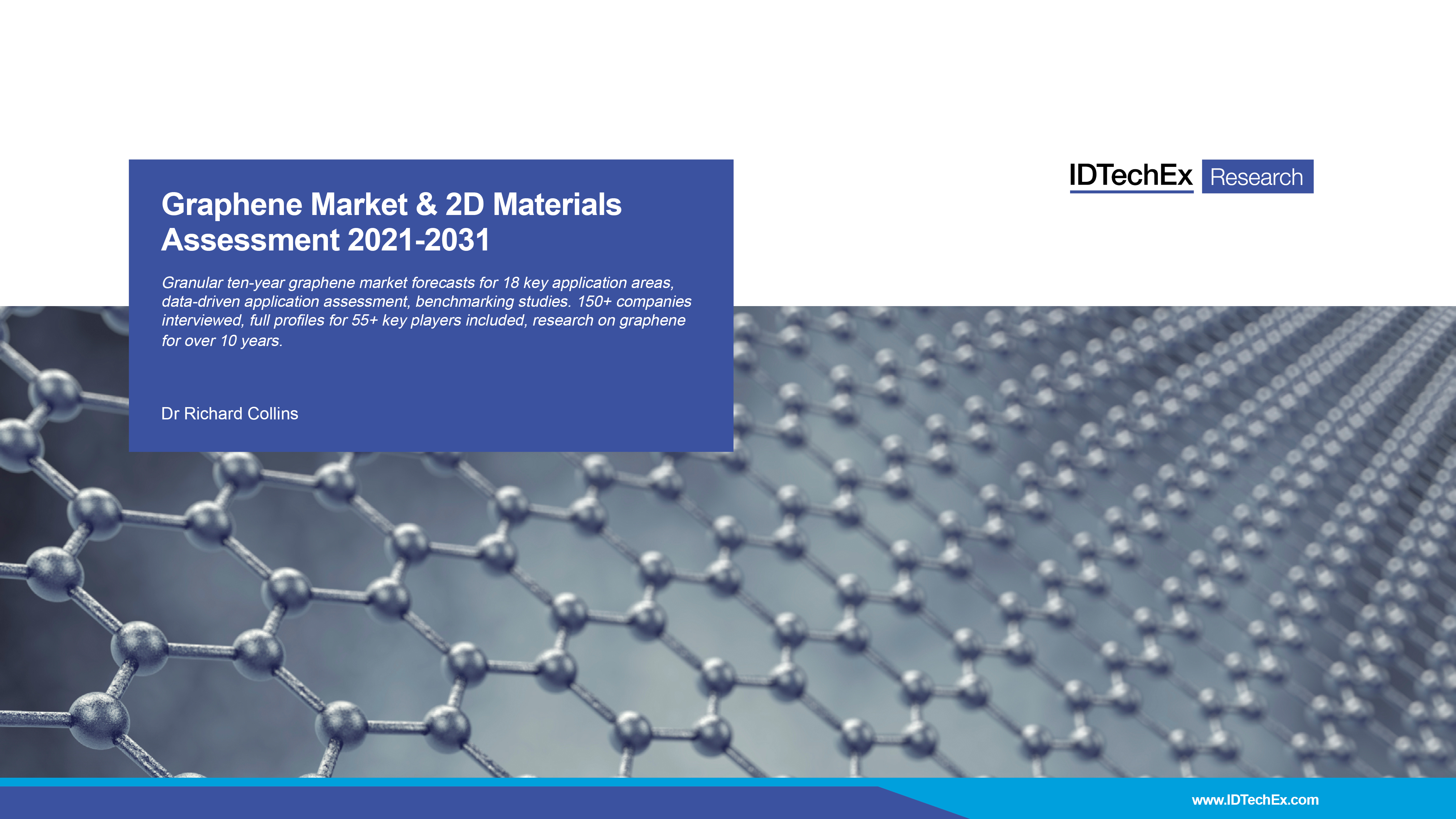
The controller of the machine was significantly changed from a normal standalone operating system to one that can act as a server in a network environment.
ADVANCED CARE SYSTEM 10.4 FREE KEY SOFTWARE
On-machine signal-based diagnostics capabilityĪ new diagnostics software module based on chaotic theory and digital signal processing was developed to assist identification of faults.Ĭommunication networks and IT systems based on client–server model To allow for failures and uncertainties, a considerable degree of sensor redundancy must to be included in the SHM system to obtain the required level of reliability. The SHM sensors must withstand high strains and severe environmental conditions for prolonged periods, for example, they must operate under temperature ranges from-50☌ to over 100☌ and cyclic strains up to 3000 microstrain for more than 10 5 cycles. Polymer matrix composite patches and reinforcement are appropriate to the embedded approach because sensors (and possibly other elements of the SHM system) can be incorporated during manufacture of the patch. Surface-mounted sensors will be exposed on the outside of the aircraft so must survive sunlight, moisture (and other aircraft fluids), erosion, and mechanical contact. Ideally, sensors should be embedded in the patch. To be considered reliable the SHM system must be durable (fatigue and moisture resistant), rugged able to survive in the aircraft environment it must also have minimum impact on the aircraft system and, as far as possible, be stand-alone and autonomous-including self-powering. The SHM system must have a high reliability and probability of detection (POD), consistent with airworthiness standards otherwise concerns with the reliability of the adhesive bond simply change to the reliability of the SHM system.

Baker, John Wang, in Aircraft Sustainment and Repair, 2018 9.4.1 SHM Requirements
